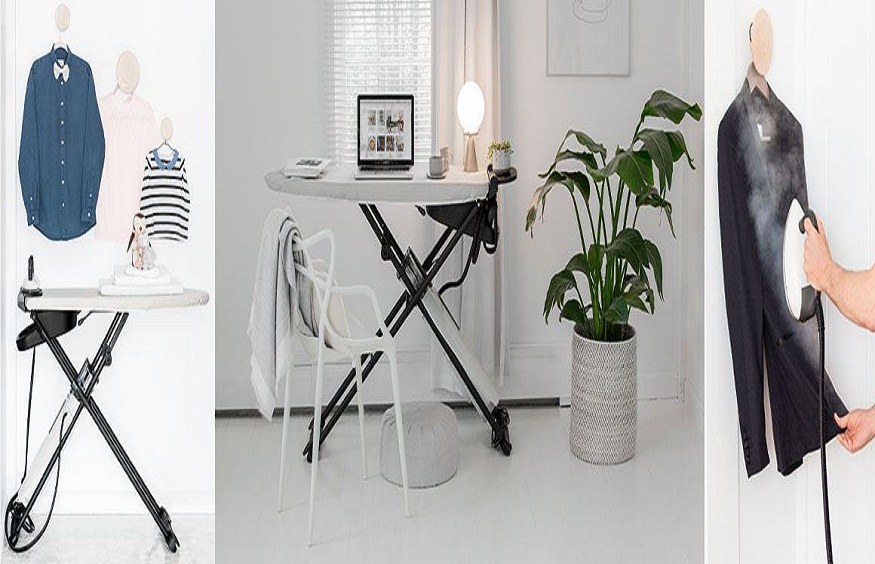
The Role of Smart Technologies in Perfecting Iron and Steel Manufacturing
In the rapidly evolving industrial landscape, the role of smart technology in transforming traditional processes cannot be overstated. This is particularly true in the steel industry, where advancements in iron-making technology and steel-making technology are setting new benchmarks for efficiency, quality, and sustainability. The digital transformation in the steel industry promises to revolutionize the sector, offering unprecedented levels of precision and control. In this blog, we will delve into how smart technologies are reshaping iron and steel manufacturing, driving operational excellence, and setting the stage for a sustainable future.
1. Smart Technology: The Game Changer
Smart technology, encompassing artificial intelligence (AI), the Internet of Things (IoT), and big data analytics, has emerged as a game-changer in the steel industry. These technologies enable real-time monitoring and predictive maintenance, significantly reducing downtime and operational costs. For instance, AI-driven predictive analytics can forecast equipment failures before they occur, allowing for preemptive maintenance that minimizes disruption.
Real-time Monitoring
Through IoT sensors, steel plants can continuously monitor various parameters such as temperature, pressure, and machinery performance. This data is then analyzed to optimize production processes, enhance product quality, and ensure safety compliance.
Predictive Maintenance
Predictive maintenance leverages AI algorithms to analyze historical data and predict future equipment failures. This proactive approach reduces unscheduled downtimes, extends the lifespan of machinery, and optimizes resource utilization.
2. Digital Transformation in Steel Industry
The digital transformation in the steel industry is not just a trend but a necessity for staying competitive in a cost-sensitive market. It involves integrating digital technologies into every facet of steel production, from raw material handling to finished goods shipping.
Enhanced Productivity
Digital twin technology—a virtual replica of physical assets—allows for real-time simulations and optimizations. By mirroring plant operations, engineers can identify bottlenecks, test scenarios, and implement solutions without disrupting actual production.
Better Quality Control
Advanced data analytics and machine learning algorithms facilitate real-time quality monitoring and control. By analyzing data from various stages of production, these technologies can spot defects and deviations early, ensuring that only top-quality products reach the market.
Sustainability Goals
Digital transformation also plays a crucial role in meeting sustainability targets. Data-driven insights help optimize energy consumption and reduce waste, driving the industry towards more environmentally friendly practices.
3. Innovations in Iron-making Technology
The iron-making process, traditionally energy-intensive and time-consuming, is undergoing significant transformation thanks to smart technology.
Hydrogen-based Reduction
One of the groundbreaking advancements is the hydrogen-based reduction method, which replaces carbon-based fuels with hydrogen. This not only reduces CO2 emissions but also enhances efficiency and output.
DR-EAF Combination
The combination of Direct Reduced Iron (DRI) and Electric Arc Furnaces (EAF) represents a leap in iron-making technology. This hybrid approach allows for lower energy consumption, reduced greenhouse gas emissions, and increased flexibility in raw material selection.
4. Advancements in Steel-making Technology
Smart technologies are equally transformative in steel-making technology, ensuring the industry meets modern demands for efficiency, quality, and sustainability.
Continuous Casting
Continuous casting, improved through smart technology, allows for more uniform and higher-quality steel production. Sensors and automated controls ensure precision in temperature and flow rates, reducing defects and enhancing output quality.
Automated Rolling Mills
Automation in rolling mills, empowered by IoT and AI, ensures consistent product dimensions and surface quality. These mills adapt in real-time to variations in raw material and process conditions, optimizing every aspect of the production process.
5. Technology and Excellence: A New Paradigm
The integration of smart technologies is not just about adopting new tools; it’s about redefining the entire operational paradigm. This technological revolution drives what we call “Technology and Excellence”.
Operational Excellence
Smart technologies enable streamlined operations, from inventory management to logistics. Real-time tracking and analytics allow for precise demand forecasting and supply chain optimization, ensuring that resources are used efficiently and cost-effectively.
Workforce Empowerment
The adoption of smart technologies also empowers the workforce, equipping them with advanced tools and knowledge. Training programs focused on digital skills ensure that employees are adept at leveraging new technologies, leading to increased productivity and job satisfaction.
6. Tata Steel Industrial Consulting (TSIC): Pioneering Change
Tata Steel, through Tata Steel Industrial Consulting (TSIC), is at the forefront of integrating smart technologies in iron and steel manufacturing. TSIC focuses on leveraging these technologies to drive operational excellence and innovation.
Specialized Training Programs
TSIC offers specialized training programs to help employees harness the power of smart technologies. These programs cover various aspects, from basic digital literacy to advanced analytics, ensuring that the workforce is well-prepared for the digital age.
Expert-Led Consultations
TSIC’s team of experts provides consultations to optimize operations using smart technologies. These consultations aim to align technological advancements with the organization’s goals, ensuring that digital transformation drives tangible benefits.
Conclusion
The role of smart technologies in perfecting iron and steel manufacturing cannot be overstated. From real-time monitoring and predictive maintenance to advanced iron-making and steel-making technologies, these innovations are setting new standards for efficiency, quality, and sustainability. The digital transformation in the steel industry is driving operational excellence and ensuring that companies remain competitive in an ever-evolving market.
Organizations like Tata Steel, through TSIC, are leading the way in this digital revolution. By offering specialized training and expert consultations, TSIC empowers the workforce and ensures that the integration of smart technologies translates into operational and strategic advantages.
In embracing these advancements, the steel industry is not only enhancing its operational capabilities but also contributing to a more sustainable and prosperous future.